Um die Leckage einer Kreiselpumpe zu verstehen, ist es wichtig, zunächst die grundlegende Funktionsweise einer Kreiselpumpe zu verstehen. Wenn die Flüssigkeit durch das Laufradauge der Pumpe eintritt und die Laufradschaufeln hinaufsteigt, hat das Fluid einen niedrigeren Druck und eine geringere Geschwindigkeit. Beim Durchströmen der Spirale steigen Druck und Geschwindigkeit an. Die Flüssigkeit tritt dann durch den Auslass aus. Dort ist der Druck hoch, die Geschwindigkeit nimmt jedoch ab. Die Flüssigkeit, die in die Pumpe hineinfließt, muss die Pumpe auch wieder verlassen. Die Pumpe erzeugt Druck, wodurch die Energie der Förderflüssigkeit erhöht wird.
Der Ausfall bestimmter Komponenten einer Kreiselpumpe, beispielsweise von Kupplungen, Hydraulikkomponenten, statischen Gelenken und Lagern, führt zum Ausfall des gesamten Systems. Ungefähr 69 Prozent aller Pumpenausfälle sind jedoch auf eine Fehlfunktion der Dichtungsvorrichtung zurückzuführen.
DIE NOTWENDIGKEIT VON GLEITRINGDICHTUNGEN
Eine Gleitringdichtungist ein Gerät zur Leckagekontrolle zwischen einer rotierenden Welle und einem flüssigkeits- oder gasgefüllten Behälter. Seine Hauptaufgabe ist die Leckagekontrolle. Alle Dichtungen lecken – sie müssen es, um einen Flüssigkeitsfilm über der gesamten Gleitringdichtungsfläche aufrechtzuerhalten. Die Leckage auf der Atmosphärenseite ist relativ gering; die Leckage eines Kohlenwasserstoffs wird beispielsweise mit einem VOC-Messgerät in ppm gemessen.
Bevor Gleitringdichtungen entwickelt wurden, dichteten Ingenieure Pumpen üblicherweise mit einer mechanischen Packung ab. Diese Packung, ein faseriges Material, das meist mit einem Schmiermittel wie Graphit imprägniert war, wurde in Abschnitte zerlegt und in eine sogenannte Stopfbuchse gesteckt. Anschließend wurde auf der Rückseite eine Stopfbuchse angebracht, um die Dichtung zu verschließen. Da die Packung direkten Kontakt mit der Welle hat, benötigt sie Schmierung, verringert aber dennoch die Leistung.
Normalerweise ermöglicht ein „Laternenring“ die Zufuhr von Spülwasser zur Packung. Dieses Wasser, das zur Schmierung und Kühlung der Welle benötigt wird, gelangt entweder in den Prozess oder in die Atmosphäre. Je nach Anwendung müssen Sie möglicherweise:
- Leiten Sie das Spülwasser vom Prozess weg, um eine Kontamination zu vermeiden.
- verhindern, dass sich Spülwasser auf dem Boden sammelt (Übersprühen), was sowohl ein Problem der OSHA als auch ein Problem der Haushaltsführung darstellt.
- Schützen Sie das Lagergehäuse vor Spülwasser, das das Öl verunreinigen und schließlich zu einem Lagerausfall führen kann.
Wie bei jeder Pumpe sollten Sie Ihre Pumpe testen, um die jährlichen Betriebskosten zu ermitteln. Eine Stopfpumpe mag zwar kostengünstig in Installation und Wartung sein, aber wenn Sie berechnen, wie viel Liter Wasser sie pro Minute oder pro Jahr verbraucht, werden Sie von den Kosten überrascht sein. Eine Pumpe mit Gleitringdichtung kann Ihnen potenziell erhebliche jährliche Kosten sparen.
Aufgrund der allgemeinen Geometrie einer Gleitringdichtung kann es überall dort, wo sich eine Dichtung oder ein O-Ring befindet, zu einer potenziellen Leckstelle kommen:
- Ein erodierter, abgenutzter oder durch Reibung beschädigter dynamischer O-Ring (oder Dichtung) bei Bewegung der Gleitringdichtung.
- Schmutz oder Verunreinigungen zwischen den Gleitringdichtungen.
- Ein nicht bestimmungsgemäßer Betrieb innerhalb der Gleitringdichtungen.
DIE FÜNF ARTEN VON VERSIEGELUNGSGERÄTEFEHLERN
Weist die Kreiselpumpe ein unkontrolliertes Leck auf, müssen Sie alle möglichen Ursachen sorgfältig prüfen, um festzustellen, ob eine Reparatur oder eine Neuinstallation notwendig ist.
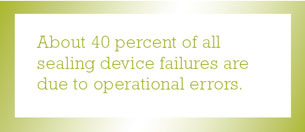
1. Betriebsstörungen
Vernachlässigung des Bestpunkts: Betreiben Sie die Pumpe am Bestpunkt (BEP) einer Leistungskurve? Jede Pumpe ist für einen bestimmten Wirkungsgrad ausgelegt. Ein Betrieb außerhalb dieses Bereichs führt zu Durchflussproblemen und damit zu Systemausfällen.
Unzureichende positive Saughöhe (NPSH): Wenn die Saughöhe Ihrer Pumpe nicht ausreicht, kann die rotierende Baugruppe instabil werden, Kavitation verursachen und zu einem Dichtungsversagen führen.
Betrieb ohne Kopf:Wenn Sie das Regelventil zu niedrig einstellen, um die Pumpe zu drosseln, kann der Durchfluss gedrosselt werden. Ein gedrosselter Durchfluss führt zu einer Rückströmung in der Pumpe, die Wärme erzeugt und zu einem Dichtungsversagen führt.
Trockenlauf und unsachgemäße Entlüftung der Dichtung: Vertikale Pumpen sind besonders anfällig, da die Gleitringdichtung oben sitzt. Bei unsachgemäßer Entlüftung kann sich Luft um die Dichtung herum festsetzen und die Stopfbuchse nicht entlüften. Läuft die Pumpe unter diesen Bedingungen weiter, versagt die Gleitringdichtung schnell.
Niedrige Dampfspanne:Es handelt sich um verdampfende Flüssigkeiten; heiße Kohlenwasserstoffe verdampfen, sobald sie atmosphärischen Bedingungen ausgesetzt werden. Wenn der Flüssigkeitsfilm über die Gleitringdichtung strömt, kann er auf der atmosphärischen Seite verdampfen und einen Ausfall verursachen. Dieser Ausfall tritt häufig bei Kesselspeisesystemen auf – heißes Wasser mit 120–130 °C verdampft aufgrund des Druckabfalls an den Dichtungsflächen.
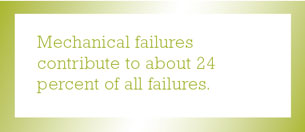
2. Mechanische Fehler
Wellenfehlausrichtung, Kupplungsunwucht und Laufradunwucht können zum Ausfall von Gleitringdichtungen beitragen. Zudem belasten falsch ausgerichtete, verschraubte Rohre die Pumpe nach der Installation stark. Vermeiden Sie außerdem einen ungeeigneten Fundamentaufbau: Ist der Fundamentaufbau sicher? Ist er ordnungsgemäß verfugt? Liegt ein Kippfuß vor? Ist er korrekt verschraubt? Überprüfen Sie abschließend die Lager. Bei zu geringer Lagertoleranz bewegen sich die Wellen und verursachen Vibrationen in der Pumpe.
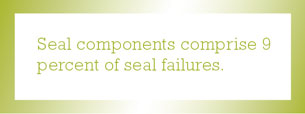
3. Dichtungskomponentenfehler
Haben Sie eine gute tribologische (reibungstheoretische) Paarung? Haben Sie die richtigen Gleitflächenkombinationen gewählt? Wie steht es um die Materialqualität der Gleitflächen? Sind Ihre Materialien für Ihre spezifische Anwendung geeignet? Haben Sie die richtigen Sekundärdichtungen wie Flachdichtungen und O-Ringe gewählt, die gegen chemische und thermische Einflüsse geschützt sind? Ihre Federn sollten nicht verstopft oder Ihre Bälge korrodiert sein. Achten Sie außerdem auf Verformungen der Gleitflächen durch Druck oder Hitze, da sich eine Gleitringdichtung unter hohem Druck verbiegt, und das verzerrte Profil kann zu Undichtigkeiten führen.
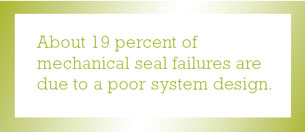
4. Systemdesignfehler
Sie benötigen eine ordnungsgemäße Dichtungsspülung und ausreichende Kühlung. Duale Systeme arbeiten mit Sperrflüssigkeiten; der zusätzliche Dichtungsbehälter muss an der richtigen Stelle platziert und mit den richtigen Instrumenten und Rohrleitungen ausgestattet sein. Berücksichtigen Sie die Länge des geraden Rohrs an der Saugseite. Ältere Pumpensysteme, die oft als Komplettpaket geliefert wurden, verfügen über einen 90°-Knie an der Saugseite, unmittelbar vor dem Eintritt des Förderstroms in das Laufradauge. Der Knie verursacht eine turbulente Strömung, die Instabilitäten in der rotierenden Baugruppe verursacht. Auch alle Saug-/Druck- und Bypass-Rohrleitungen müssen korrekt ausgeführt sein, insbesondere wenn einige Rohre im Laufe der Jahre repariert wurden.
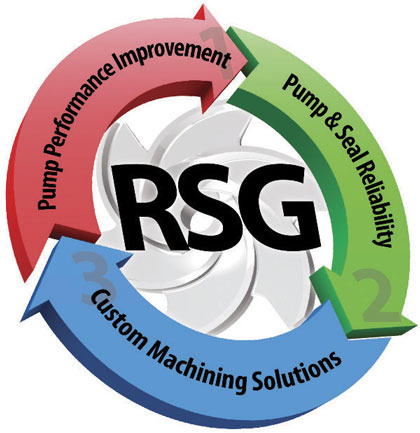
5. Alles andere
Sonstige Faktoren machen nur etwa 8 Prozent aller Ausfälle aus. Beispielsweise sind manchmal Zusatzsysteme erforderlich, um eine akzeptable Betriebsumgebung für eine Gleitringdichtung zu gewährleisten. Bei dualen Systemen wird eine Zusatzflüssigkeit als Barriere benötigt, die verhindert, dass Verunreinigungen oder Prozessflüssigkeit in die Umgebung gelangen. Für die meisten Anwender bietet jedoch eine der ersten vier Kategorien die passende Lösung.
ABSCHLUSS
Gleitringdichtungen sind ein wichtiger Faktor für die Zuverlässigkeit rotierender Maschinen. Sie sind für Leckagen und Systemausfälle verantwortlich, weisen aber auch auf Probleme hin, die später zu schweren Schäden führen können. Die Zuverlässigkeit der Dichtung wird maßgeblich von der Dichtungskonstruktion und der Betriebsumgebung beeinflusst.
Veröffentlichungszeit: 26. Juni 2023