Gleitringdichtungenspielen eine sehr wichtige Rolle bei der Vermeidung von Leckagen für viele verschiedene Branchen. In der Schifffahrt gibt esGleitringdichtungen für Pumpen, rotierende Wellen-Gleitringdichtungen. Und in der Öl- und Gasindustrie gibt esPatronen-Gleitringdichtungen,Geteilte Gleitringdichtungen oder Trockengas-Gleitringdichtungen. In der Automobilindustrie gibt es Wasser-Gleitringdichtungen. Und in der chemischen Industrie gibt es Mischer-Gleitringdichtungen (Rührwerk-Gleitringdichtungen) und Kompressor-Gleitringdichtungen.
Abhängig von den unterschiedlichen Einsatzbedingungen ist eine Gleitringdichtung mit unterschiedlichem Material erforderlich. Es gibt viele Arten von Materialien, die in derGleitringdichtungen wie z. B. Keramik-Gleitringdichtungen, Kohle-Gleitringdichtungen, Silikonkarbid-Gleitringdichtungen,SSIC Gleitringdichtungen undTC Gleitringdichtungen.
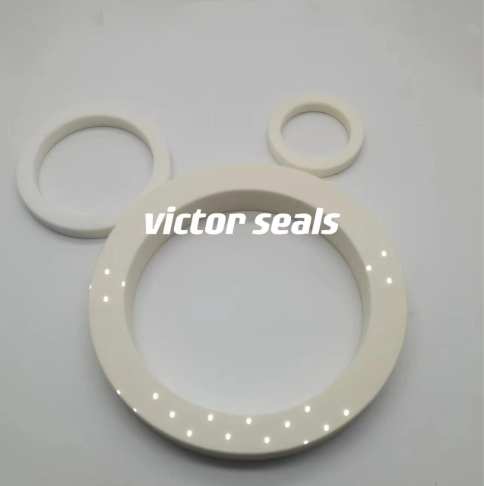
Keramische Gleitringdichtungen
Keramische Gleitringdichtungen sind wichtige Komponenten in verschiedenen industriellen Anwendungen. Sie verhindern das Austreten von Flüssigkeiten zwischen zwei Oberflächen, beispielsweise einer rotierenden Welle und einem stationären Gehäuse. Diese Dichtungen werden aufgrund ihrer außergewöhnlichen Verschleißfestigkeit, Korrosionsbeständigkeit und Widerstandsfähigkeit gegenüber extremen Temperaturen sehr geschätzt.
Die Hauptaufgabe keramischer Gleitringdichtungen besteht darin, die Integrität von Anlagen zu gewährleisten, indem sie Flüssigkeitsverlust oder Verunreinigungen verhindern. Sie werden in zahlreichen Branchen eingesetzt, darunter in der Öl- und Gasindustrie, der chemischen Verarbeitung, der Wasseraufbereitung, der Pharma- und Lebensmittelindustrie. Die weite Verbreitung dieser Dichtungen ist auf ihre langlebige Konstruktion zurückzuführen; sie bestehen aus fortschrittlichen Keramikwerkstoffen, die im Vergleich zu anderen Dichtungsmaterialien überlegene Leistungsmerkmale bieten.
Keramische Gleitringdichtungen bestehen aus zwei Hauptkomponenten: einer mechanischen Gleitfläche (üblicherweise aus Keramik) und einer mechanischen Gleitfläche (üblicherweise aus Kohlenstoffgraphit). Die Dichtwirkung entsteht, wenn beide Flächen durch Federkraft zusammengepresst werden, wodurch eine wirksame Barriere gegen Flüssigkeitslecks entsteht. Im Betrieb reduziert der Schmierfilm zwischen den Dichtflächen Reibung und Verschleiß und sorgt gleichzeitig für eine dichte Abdichtung.
Ein entscheidender Faktor, der keramische Gleitringdichtungen von anderen Dichtungstypen unterscheidet, ist ihre hervorragende Verschleißfestigkeit. Keramikmaterialien verfügen über hervorragende Härteeigenschaften, die es ihnen ermöglichen, abrasiven Bedingungen ohne nennenswerte Schäden standzuhalten. Dies führt zu langlebigeren Dichtungen, die seltener ausgetauscht oder gewartet werden müssen als Dichtungen aus weicheren Materialien.
Neben der Verschleißfestigkeit zeichnen sich Keramiken auch durch eine außergewöhnliche thermische Stabilität aus. Sie halten hohen Temperaturen stand, ohne dass ihre Dichtwirkung nachlässt. Dadurch eignen sie sich für den Einsatz in Hochtemperaturanwendungen, bei denen andere Dichtungsmaterialien vorzeitig versagen könnten.
Darüber hinaus bieten keramische Gleitringdichtungen eine hervorragende chemische Verträglichkeit und Beständigkeit gegenüber verschiedenen korrosiven Substanzen. Dies macht sie zu einer attraktiven Wahl für Branchen, die regelmäßig mit aggressiven Chemikalien und Flüssigkeiten arbeiten.
Keramische Gleitringdichtungen sind unerlässlichKomponentendichtungenEntwickelt, um Flüssigkeitslecks in Industrieanlagen zu verhindern. Ihre einzigartigen Eigenschaften wie Verschleißfestigkeit, thermische Stabilität und chemische Verträglichkeit machen sie zur bevorzugten Wahl für verschiedene Anwendungen in zahlreichen Branchen
Physikalische Eigenschaften von Keramik | ||||
Technische Parameter | Einheit | 95 % | 99 % | 99,50 % |
Dichte | g/cm3 | 3.7 | 3,88 | 3.9 |
Härte | HRA | 85 | 88 | 90 |
Porositätsrate | % | 0,4 | 0,2 | 0,15 |
Bruchfestigkeit | MPa | 250 | 310 | 350 |
Wärmeausdehnungskoeffizient | 10(-6)/K | 5.5 | 5.3 | 5.2 |
Wärmeleitfähigkeit | W/MK | 27,8 | 26,7 | 26 |
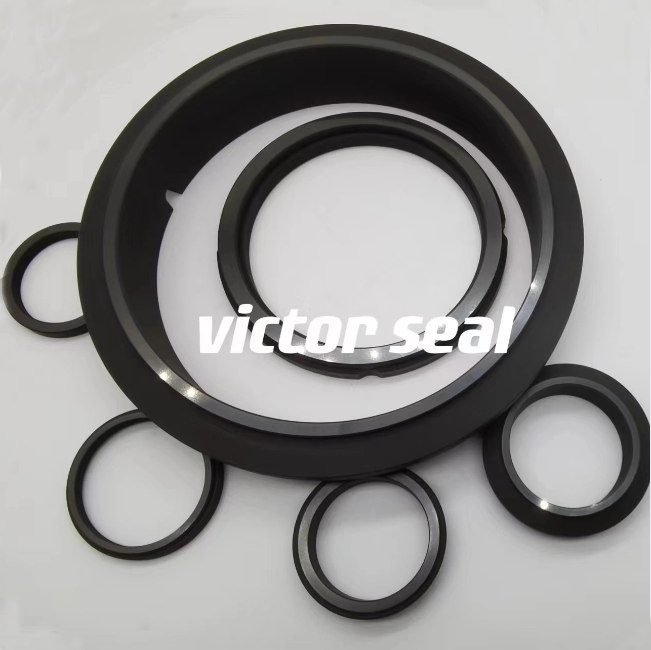
Kohlenstoff-Gleitringdichtungen
Mechanische Kohlenstoffdichtungen haben eine lange Geschichte. Graphit ist eine Isoform des Elements Kohlenstoff. 1971 wurde in den USA das flexible Graphit-Gleitringdichtungsmaterial erfolgreich untersucht, das das Problem der Undichtigkeit von Atomventilen löste. Nach der Tiefenverarbeitung wird der flexible Graphit zu einem hervorragenden Dichtungsmaterial, aus dem verschiedene Kohlenstoff-Gleitringdichtungen mit der Wirkung von Dichtungskomponenten hergestellt werden. Diese Kohlenstoff-Gleitringdichtungen werden in der Chemie-, Erdöl- und Stromindustrie beispielsweise als Hochtemperatur-Flüssigkeitsdichtung eingesetzt.
Da der flexible Graphit durch die Ausdehnung von expandiertem Graphit nach hohen Temperaturen gebildet wird, ist die Menge des im flexiblen Graphit verbleibenden Interkalationsmittels sehr gering, jedoch nicht vollständig. Daher haben das Vorhandensein und die Zusammensetzung des Interkalationsmittels einen großen Einfluss auf die Qualität und Leistung des Produkts.
Auswahl des Kohlenstoff-Dichtflächenmaterials
Der ursprüngliche Erfinder verwendete konzentrierte Schwefelsäure als Oxidationsmittel und Interkalationsmittel. Es zeigte sich jedoch, dass nach dem Auftragen auf die Dichtung einer Metallkomponente eine kleine Menge Schwefel, die im flexiblen Graphit verblieb, das Kontaktmetall bei längerem Gebrauch korrodierte. Angesichts dieses Problems versuchten einige einheimische Wissenschaftler, das Verfahren zu verbessern, wie beispielsweise Song Kemin, der Essigsäure und organische Säure anstelle von Schwefelsäure wählte. Säure, langsam in Salpetersäure und bei Abkühlung auf Raumtemperatur, hergestellt aus einer Mischung aus Salpetersäure und Essigsäure. Unter Verwendung der Mischung aus Salpetersäure und Essigsäure als Einfügemittel wurde der schwefelfreie expandierte Graphit mit Kaliumpermanganat als Oxidationsmittel hergestellt und Essigsäure langsam zu Salpetersäure gegeben. Die Temperatur wird auf Raumtemperatur gesenkt und die Mischung aus Salpetersäure und Essigsäure hergestellt. Dann werden der natürliche Flockengraphit und Kaliumpermanganat zu dieser Mischung gegeben. Unter ständigem Rühren wird die Temperatur auf 30 °C eingestellt. Nach einer Reaktionszeit von 40 Minuten wird das Wasser neutral gewaschen und bei 50–60 °C getrocknet. Durch die Hochtemperaturexpansion wird expandierter Graphit hergestellt. Bei dieser Methode wird keine Vulkanisation erreicht, solange das Produkt ein bestimmtes Expansionsvolumen erreicht, wodurch eine relativ stabile Beschaffenheit des Dichtungsmaterials erreicht wird.
Typ | M106H | M120H | M106K | M120K | M106F | M120F | M106D | M120D | M254D |
Marke | Imprägniert | Imprägniert | Imprägniertes Phenol | Antimon Kohlenstoff (A) | |||||
Dichte | 1,75 | 1.7 | 1,75 | 1.7 | 1,75 | 1.7 | 2.3 | 2.3 | 2.3 |
Bruchfestigkeit | 65 | 60 | 67 | 62 | 60 | 55 | 65 | 60 | 55 |
Druckfestigkeit | 200 | 180 | 200 | 180 | 200 | 180 | 220 | 220 | 210 |
Härte | 85 | 80 | 90 | 85 | 85 | 80 | 90 | 90 | 65 |
Porosität | <1 | <1 | <1 | <1 | <1 | <1 | <1,5 | <1,5 | <1,5 |
Temperaturen | 250 | 250 | 250 | 250 | 250 | 250 | 400 | 400 | 450 |
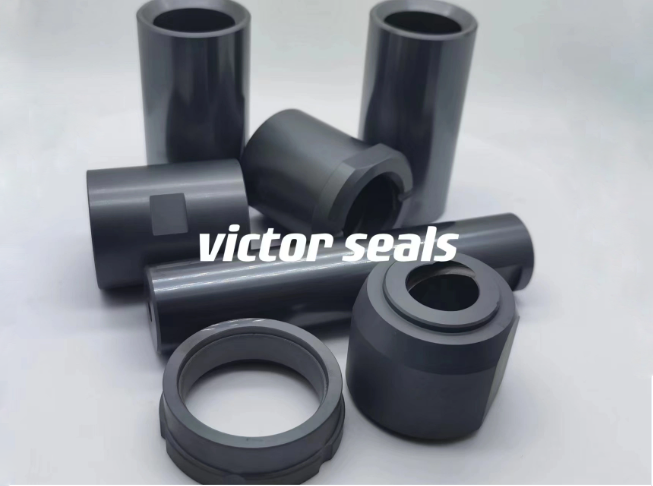
Gleitringdichtungen aus Siliziumkarbid
Siliziumkarbid (SiC) ist auch als Carborund bekannt und wird aus Quarzsand, Petrolkoks (oder Kohlekoks), Holzspänen (die bei der Herstellung von grünem Siliziumkarbid hinzugefügt werden müssen) usw. hergestellt. Siliziumkarbid enthält auch ein seltenes Mineral in der Natur: Maulbeere. In modernen C-, N-, B- und anderen nichtoxidischen hochtechnologischen feuerfesten Rohstoffen ist Siliziumkarbid eines der am häufigsten verwendeten und wirtschaftlichsten Materialien und kann als Goldstahlsand oder feuerfester Sand bezeichnet werden. Derzeit ist Chinas industrielle Produktion von Siliziumkarbid in schwarzes Siliziumkarbid und grünes Siliziumkarbid unterteilt. Beide sind hexagonale Kristalle mit einem Anteil von 3,20 bis 3,25 und einer Mikrohärte von 2840 bis 3320 kg/m²
Siliziumkarbidprodukte werden je nach Anwendungsumgebung in viele Arten eingeteilt. Es wird im Allgemeinen eher mechanisch verwendet. Beispielsweise ist Siliziumkarbid aufgrund seiner guten chemischen Korrosionsbeständigkeit, hohen Festigkeit, hohen Härte, guten Verschleißfestigkeit, des geringen Reibungskoeffizienten und der hohen Temperaturbeständigkeit ein ideales Material für Gleitringdichtungen aus Siliziumkarbid.
SIC-Dichtungsringe lassen sich in statische, bewegliche und flache Ringe unterteilen. Aus SiC-Silizium lassen sich je nach Kundenwunsch verschiedene Hartmetallprodukte herstellen, wie z. B. Siliziumkarbid-Drehringe, Siliziumkarbid-Festsitze und Siliziumkarbid-Buchsen. SiC-Silizium kann auch in Kombination mit Graphit verwendet werden. Der Reibungskoeffizient ist geringer als bei Aluminiumoxidkeramik und Hartmetalllegierungen, sodass SiC-Silizium bei hohen PV-Werten, insbesondere bei starker Säure- und Alkalibelastung, eingesetzt werden kann.
Die geringere Reibung von SIC ist einer der Hauptvorteile des Einsatzes in Gleitringdichtungen. SIC ist daher verschleißbeständiger als andere Materialien und verlängert so die Lebensdauer der Dichtung. Darüber hinaus verringert die geringere Reibung von SIC den Schmierbedarf. Mangelnde Schmierung verringert das Risiko von Verunreinigungen und Korrosion und verbessert so Effizienz und Zuverlässigkeit.
SIC zeichnet sich außerdem durch eine hohe Verschleißfestigkeit aus. Dies bedeutet, dass es Dauereinsatz standhält, ohne sich abzunutzen oder zu brechen. Dies macht es zum perfekten Material für Anwendungen, die ein hohes Maß an Zuverlässigkeit und Haltbarkeit erfordern.
Es kann auch nachgeläppt und poliert werden, sodass eine Dichtung im Laufe ihrer Lebensdauer mehrmals erneuert werden kann. Es wird im Allgemeinen eher mechanisch verwendet, beispielsweise in Gleitringdichtungen, da es eine gute chemische Korrosionsbeständigkeit, hohe Festigkeit, hohe Härte, gute Verschleißfestigkeit, einen kleinen Reibungskoeffizienten und eine hohe Temperaturbeständigkeit aufweist.
Bei der Verwendung von Siliziumkarbid für Gleitringdichtungen verbessert sich die Leistung, die Lebensdauer der Dichtungen, die Wartungskosten und die Betriebskosten rotierender Maschinen wie Turbinen, Kompressoren und Kreiselpumpen. Siliziumkarbid kann je nach Herstellungsverfahren unterschiedliche Eigenschaften aufweisen. Reaktionsgebundenes Siliziumkarbid entsteht durch die Bindung von Siliziumkarbidpartikeln in einem Reaktionsprozess.
Dieser Prozess beeinflusst die meisten physikalischen und thermischen Eigenschaften des Materials nicht wesentlich, schränkt jedoch dessen chemische Beständigkeit ein. Die häufigsten problematischen Chemikalien sind Ätzmittel (und andere Chemikalien mit hohem pH-Wert) und starke Säuren. Daher sollte reaktionsgebundenes Siliziumkarbid bei diesen Anwendungen nicht verwendet werden.
Reaktionsgesintert infiltriertSiliziumkarbid. Bei diesem Material werden die Poren des ursprünglichen SiC-Materials im Infiltrationsprozess durch Ausbrennen von metallischem Silizium gefüllt. Dadurch entsteht sekundäres SiC, das dem Material außergewöhnliche mechanische Eigenschaften verleiht und es verschleißfest macht. Dank seiner minimalen Schrumpfung kann es zur Herstellung großer und komplexer Teile mit engen Toleranzen verwendet werden. Der Siliziumgehalt begrenzt jedoch die maximale Betriebstemperatur auf 1.350 °C, die chemische Beständigkeit ist auf einen pH-Wert von ca. 10 begrenzt. Der Einsatz des Materials in aggressiven alkalischen Umgebungen wird nicht empfohlen.
GesintertSiliziumkarbid wird durch Sintern eines vorverdichteten, sehr feinen SIC-Granulats bei einer Temperatur von 2000 °C gewonnen, wodurch starke Bindungen zwischen den Körnern des Materials entstehen.
Zuerst verdickt sich das Gitter, dann nimmt die Porosität ab und schließlich sintern die Bindungen zwischen den Körnern. Bei einer solchen Verarbeitung kommt es zu einer erheblichen Schrumpfung des Produkts – um etwa 20 %.
SSIC-Dichtungsring ist beständig gegen alle Chemikalien. Da in seiner Struktur kein metallisches Silizium vorhanden ist, kann es bei Temperaturen bis zu 1600 °C verwendet werden, ohne dass seine Festigkeit beeinträchtigt wird
Eigenschaften | R-SiC | S-SiC |
Porosität (%) | ≤0,3 | ≤0,2 |
Dichte (g/cm3) | 3.05 | 3,1 bis 3,15 |
Härte | 110~125 (HS) | 2800 (kg/mm2) |
Elastizitätsmodul (Gpa) | ≥400 | ≥410 |
SiC-Gehalt (%) | ≥85 % | ≥99 % |
Si-Gehalt (%) | ≤15 % | 0,10 % |
Biegefestigkeit (Mpa) | ≥350 | 450 |
Druckfestigkeit (kg/mm2) | ≥2200 | 3900 |
Wärmeausdehnungskoeffizient (1/℃) | 4,5×10-6 | 4,3×10-6 |
Hitzebeständigkeit (in der Atmosphäre) (℃) | 1300 | 1600 |
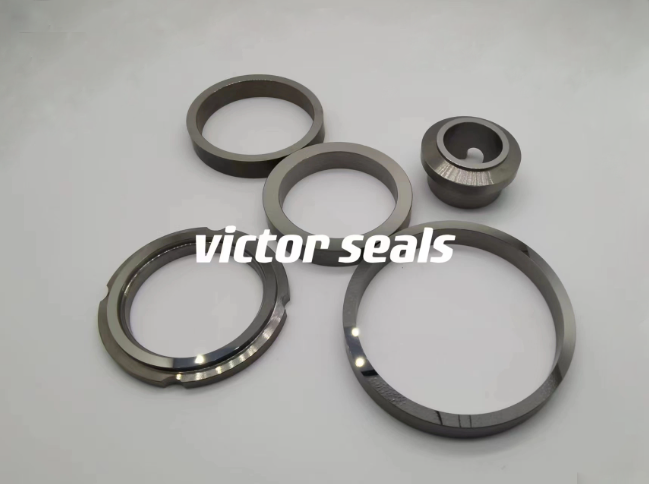
TC-Gleitringdichtung
TC-Materialien zeichnen sich durch hohe Härte, Festigkeit, Abriebfestigkeit und Korrosionsbeständigkeit aus. Sie werden auch als „Industriezahn“ bezeichnet. Aufgrund ihrer überlegenen Leistung finden sie breite Anwendung in der Rüstungsindustrie, der Luft- und Raumfahrt, der mechanischen Verarbeitung, der Metallurgie, der Ölförderung, der elektronischen Kommunikation, der Architektur und anderen Bereichen. Beispielsweise werden Wolframkarbidringe in Pumpen, Kompressoren und Rührwerken als Gleitringdichtungen eingesetzt. Dank ihrer guten Abriebfestigkeit und hohen Härte eignen sie sich für die Herstellung verschleißfester Teile mit hoher Temperaturbeständigkeit, Reibung und Korrosion.
Entsprechend seiner chemischen Zusammensetzung und seinen Verwendungseigenschaften kann TC in vier Kategorien unterteilt werden: Wolframkobalt (YG), Wolframtitan (YT), Wolframtitantantal (YW) und Titancarbid (YN).
Die Hartlegierung Wolfram-Kobalt (YG) besteht aus WC und Co. Sie eignet sich zur Bearbeitung spröder Werkstoffe wie Gusseisen, Nichteisenmetalle und nichtmetallische Werkstoffe.
Stellit (YT) besteht aus WC, TiC und Co. Durch die Zugabe von TiC zur Legierung wird die Verschleißfestigkeit verbessert, jedoch nehmen Biegefestigkeit, Schleifleistung und Wärmeleitfähigkeit ab. Aufgrund seiner Sprödigkeit bei niedrigen Temperaturen eignet es sich nur für die Hochgeschwindigkeitszerspanung allgemeiner Werkstoffe und nicht für die Bearbeitung spröder Werkstoffe.
Wolfram, Titan, Tantal (Niob) und Kobalt (YW) werden der Legierung zugesetzt, um durch entsprechende Mengen Tantalkarbid oder Niobkarbid die Härte bei hohen Temperaturen, die Festigkeit und die Abriebfestigkeit zu erhöhen. Gleichzeitig wird die Zähigkeit verbessert und die Schneidleistung insgesamt verbessert. Es wird hauptsächlich für harte Schneidmaterialien und intermittierendes Schneiden verwendet.
Die karbonisierte Titanbasisklasse (YN) ist eine Hartlegierung mit der Hartphase TiC, Nickel und Molybdän. Ihre Vorteile sind hohe Härte, Antihaftfähigkeit, Anti-Sichelverschleiß und Antioxidationsfähigkeit. Bei Temperaturen über 1000 Grad ist sie noch bearbeitbar. Sie eignet sich für die kontinuierliche Endbearbeitung von legiertem Stahl und Vergütungsstahl.
Modell | Nickelgehalt (Gew.-%) | Dichte (g/cm²) | Härte (HRA) | Biegefestigkeit (≥N/mm²) |
YN6 | 5,7-6,2 | 14,5-14,9 | 88,5-91,0 | 1800 |
YN8 | 7,7-8,2 | 14,4-14,8 | 87,5-90,0 | 2000 |
Modell | Kobaltgehalt (Gew.-%) | Dichte (g/cm²) | Härte (HRA) | Biegefestigkeit (≥N/mm²) |
YG6 | 5,8-6,2 | 14,6-15,0 | 89,5-91,0 | 1800 |
YG8 | 7,8-8,2 | 14,5-14,9 | 88,0-90,5 | 1980 |
YG12 | 11,7-12,2 | 13,9-14,5 | 87,5-89,5 | 2400 |
YG15 | 14,6-15,2 | 13,9-14,2 | 87,5-89,0 | 2480 |
YG20 | 19,6-20,2 | 13,4-13,7 | 85,5-88,0 | 2650 |
YG25 | 24,5-25,2 | 12,9-13,2 | 84,5-87,5 | 2850 |